
Qualifying a transport box or container is much more complex than qualifying a refrigerator. Since the object to be qualified moves around in uncontrolled environments, we first need clarity on the planned purpose of the box and container by answering the following two questions: is it a road, air or ocean shipment? How long will the shipment take? The following picture shows an overview of different transport modes:
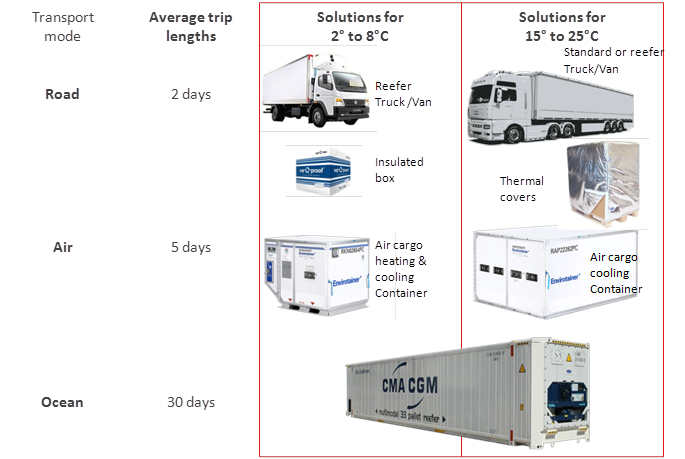
When performing a qualification of a transport box or container, another challenge is to come up with a realistic temperature profile to test against. How long will the shipment take? What temperatures will be expected at origin, on the way and at destination? Are there seasonal changes? There are two approaches to define the correct ambient temperature profile:
- Use empirical data: A common approach is to classify the shipment into sections (origin to hub; hub to hub; hub to destination), or to cluster them by assigning climatic zones to the sections (e.g. cold, moderate, warm, hot) and to define extreme seasonal weather changes (e.g. cold to hot, hot to cold). The difficulty with this approach is to define the specific length of each shipment section (how many hours the product has in each section) and estimate a realistic average temperature within each climate zone.
- Map the ambient temperature: In reality, this is the best way is to measure the temperature of a specific route. This is done by performing several seasonal shipments and collecting the temperature data from each of the shipments. Afterwards the average temperatures from each shipment section are calculated and used. This is also the most elaborate method.
Last, but not least, there is a significant difference between passive insulated boxes using phase change materials (PCM) with insulation and active heating/cooling containers. From a qualification perspective the difference of the two technologies is not so much performance, but rather the risks which need to be considered. The following explains the differences between the two technologies including a high-level risk appraisal.
Passive Insulated Box
- Technology Used: Thermal Packs filled with Phase Change Material (PCM) having a defined melting point (5°C melting point for 2-8°C shipments) and insulation materials such as Vacuum Panels.
- Process at Origin: Phase Change Material (PCM) must be pre-conditioned and must have the right temperature when loaded. To ensure the promised performance the box must be built-up exactly as designed: product surrounded by one layer (minimum) of PCM, surrounded by one layer (minimum) of Vacuum Panels, held together by a cardboard box.
- Process During Shipment: Ensure the shipment is not exceeding the defined shipment lengths. For example, if the box is built to keep temperature for 72 hours, a longer shipment time could result in damaging the goods.
High-level Risk Appraisal: The highest risk is a packaging error (e.g. wrong conditioning of PCM). As soon as a shipment is on its way, the solution is very stable and there are only minimal risks.
Active Container
- Technology Used: Insulated container with air ventilation, heating and cooling unit (typically compressor cooling and electrical heating) and battery including a charging unit.
- Process at Origin: The battery must be charged before loading and the right set temperature must be defined.
- Process During Shipment: Re-charge the unit at hubs and airports. Prevent manipulation of the set temperature or door openings.
High-level Risk Appraisal: While active containers are very easy to load, there are significant risks during shipment involving human error (e.g. no recharging) and mechanical failure. Heating and cooling containers consist of hundreds of mechanical and electronic components which have the potential to fail.
As soon as the box or container has been chosen, and the intended purpose is defined, qualification can start by applying the steps of the V-Model:
- Define Specifications of the transport box or container by describing the type transport box, loading volume, set temperature, shipment lengths of the transport box or container and specific temperature profiles.
- Conduct the Risk Analysis describing all operational and technical risks of the transport box or container.
- Perform Operational Qualification by testing the box in a Climate Chamber (Mapping) running through all defined temperature profiles.
- Conduct Qualification by performing test shipments (Mapping) on a specified route (e.g. shipment from an extreme cold environment to an extreme hot environment).